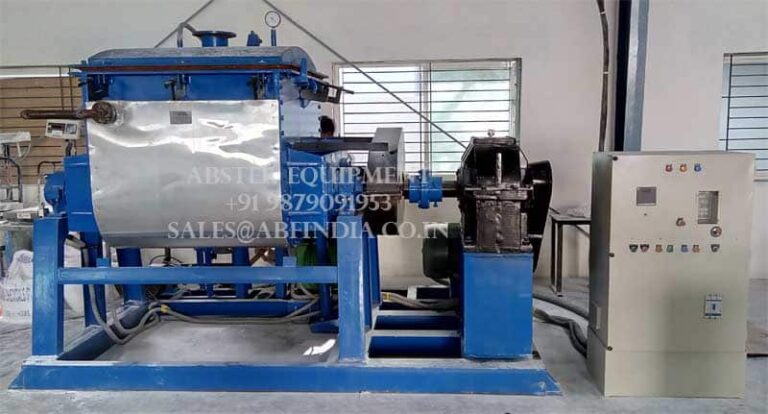
Hydraulic Mixer and Kneader for Htv Rubber Silicone Butyl Glue Bubble Gum
RTV sealant vacuum power mixer
Summary:
Vacuum Kneader is ideal high-performance equipment for mixing and kneading high viscosity and super high viscosity materials. Vacuum kneader is widely used in the industry, inclusive of high viscosity sealants, silicone rubber.CMC, batteries, inks, dyes, pharmaceuticals, resins, plastics and cosmetics, etc. It is ideal equipment for production of ink, pigment, adhesive sealant, paste, paste-type material, lubricant, paint, paste cosmetics, emulsion, cream food and additive, etc
What is the key features and components of a sigma mixer?
Dual Mixing Blades: The sigma mixer features two horizontally oriented, sigma-shaped blades that rotate in opposite directions. These blades resemble the Greek letter “sigma,” which gives the mixer its name.
Trough or Bowl: The mixing chamber of the sigma mixer is typically a trough or bowl-shaped vessel where the materials are loaded for mixing. The dual blades rotate within this chamber, ensuring thorough mixing and kneading.
Cooling or Heating Jackets: Some sigma mixers are equipped with cooling or heating jackets around the mixing chamber. These jackets allow for precise temperature control during mixing processes that involve temperature-sensitive materials.
Control System: Modern sigma mixers often include control systems that allow operators to adjust the mixing speed, direction of rotation, and other parameters for optimal mixing performance.
What is the working principle of sigma mixer?
Kneading and cutting: The relative movement of the sigma mixer’s 2 blades triggers the kneading, cutting and folding of the material. This action mixes the different material components together, ensuring even dispersion.
What is the benefits of using sigma mixer?
Effective Mixing: The dual-blade design and kneading action ensure thorough and consistent mixing even for high-viscosity materials.
Heat Transfer: Cooling or heating jackets allow for precise temperature control during mixing processes.
Versatility: Sigma mixers can handle a wide range of materials, from sticky pastes to dry powders.